Gravity Casting at Align MFG
At Align MFG, our expertise in aluminium gravity casting is unmatched, providing specialized solutions for pivotal industry applications. With factories across the United States, Thailand, Vietnam, and India, we are uniquely positioned to handle complex projects in the Oil & Gas, Railway, and Construction sectors. Our commitment to quality and precision places us at the forefront of metal manufacturing.
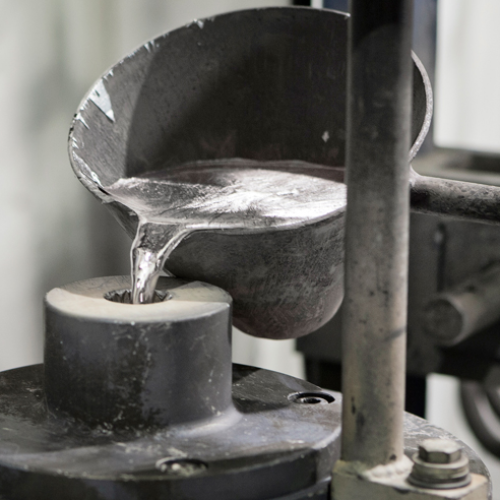
The Aluminum Gravity Casting Process
Align MFG utilizes the Aluminum Gravity Casting Process to produce precise aluminium parts that meet stringent quality standards for U.S. industries as well as global applications. This process involves pouring molten aluminium into molds, using gravity to ensure thorough and accurate mold filling.
This technique is crucial for creating complex, detailed components with excellent surface finishes and dimensional accuracy. Align MFG's engineering capabilities underscores their commitment to delivering strong, lightweight aluminium components tailored to the specific needs of diverse industries such as Oil & Gas, Railway, Construction and beyond.
FAQ
Gravity casting involves pouring molten metal into a mold and allowing it to flow naturally by gravity rather than using external pressure. Unlike high-pressure casting, gravity casting is a slower, gentler process, which reduces the risk of metal turbulence and defects, leading to improved structural integrity and a smoother finish in the final part.
Gravity casting is commonly used for parts that require strong, dense structures, such as automotive engine components, valve bodies, and gear housings. It’s also widely used for decorative items and furniture fittings, where a smooth surface and durability are essential.
Aluminum, brass, and zinc alloys are ideal for gravity casting. Aluminum is lightweight and corrosion-resistant, brass offers strength and wear resistance, and zinc provides good fluidity and dimensional stability. These metals contribute to high-quality parts with smooth surfaces, excellent detail, and longevity.
Gravity casting allows for uniform metal flow into the mold, reducing internal stresses and creating a dense, durable structure. This process improves the part’s structural integrity, making it more resistant to wear, corrosion, and deformation over time, which enhances the lifespan of the product.
Gravity casting is cost-effective for medium to high-volume runs because it requires relatively simple mold designs and minimal maintenance. The molds can be reused for many cycles, and the slower, steady pouring process reduces waste, making it an economical choice for producing high-quality parts at scale.
Ready to discuss
your metal Gravity Casting project with Align MFG?
Our team is eager to assist you whether you're based in the United States or internationally. Contact us today to request a quote or learn more about how our gravity casting services can impeccably meet your project requirements. We're here to collaborate with you to achieve precision in every aspect of your projects.